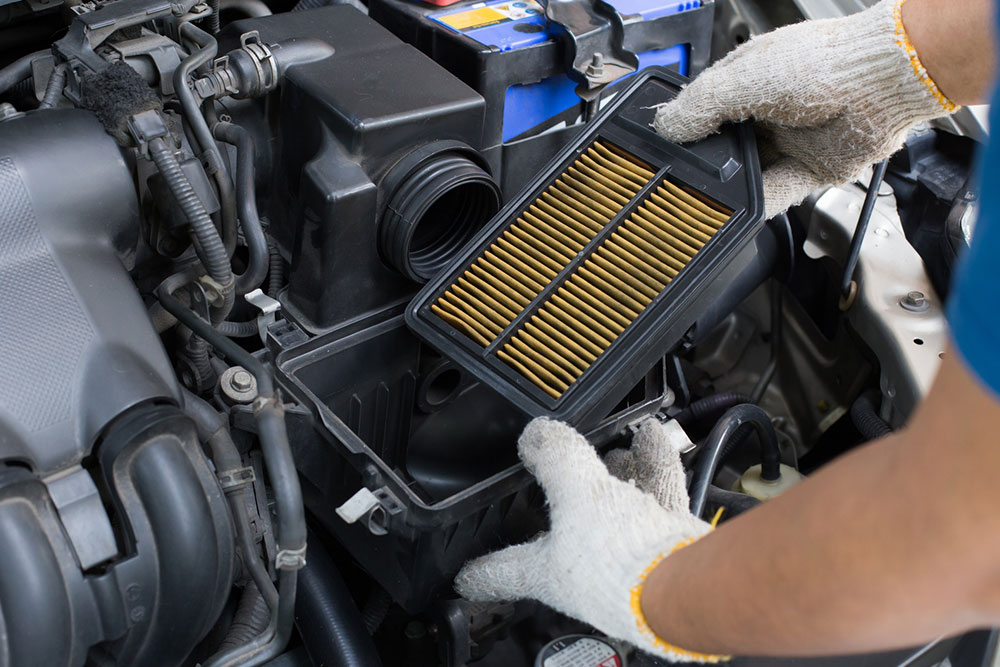
9 tips to maintain industrial machines optimally
Factories and industries need adequate and updated machinery to function properly. From manufacturing and processing to packaging and labeling, machines are needed at every stage of production, which means industries are heavily dependent on their smooth functioning. Proper machinery maintenance in factories is a must to ensure that the production of goods is not affected at any stage. Here are some tips that may come in handy for factories and industries when handling industrial machines.
Don’t miss calibration checks
An industrial machine has many different parts that work together to perform the required task. So, if even one of these parts doesn’t function adequately, the machine may lag or stop working. For this reason, factories need to carry out regular calibration checks, with the frequency depending on the type of machine and its functions. Basically, calibration checks compare the readings on a particular machine against a standard set for machines of its type. This helps understand whether the machine is performing well or has any defective or malfunctioning parts. The machine’s manufacturing company or a technician should be able to reveal how frequent its calibration checks should be.
Clean the machine frequently
Even if a factory is cleaned and well maintained, the machines being operated in the factory are vulnerable to rust, corrosion, and wear and tear. So, regularly cleaning industrial machines is a part of the maintenance process. Sometimes, one may require a micro-abrasive cleaner to access spots that are difficult to reach. Such products ensure deep cleaning of the machine’s surfaces without damaging it. But one needs to look for micro-abrasive cleaners of good quality, so that they do not cause any damage to the product. Also, it is advisable to apply a rust-preventative coating after cleaning to eliminate any chances of rust developing on the machine’s surface.
Get machines tested if they have been out of use for long
Often, factories may not require certain machines very frequently, so these may be stored away for the most part. But when these machines are taken out for use again, they should be thoroughly tested before they are used. Infrequent use of a machine makes it highly susceptible to rust and corrosion. Also, some of its parts may not function as efficiently as they might have when the machine was new. Thus, factories should check the lubricants in such machines and change them if required. Also, they should carefully clean out any dust particles, grease, or oil accumulated on the machine’s surface. A recalibration check may also be required.
Address any issues proactively
Prevention is always better than cure, even when it comes to industrial machines. A machine may have only a small issue at present, but it might escalate to a major one if one does not address it immediately. For example, if a machine produces unusual grinding or screeching noises, it might mean that it needs to be lubricated. Detecting such issues early on can save one from costly repair work or accidents in the future. A technician should be called on to check the machines every once in a while.
Understand what issues a machine is most likely to develop
One way to prevent problems with industrial machines is to predict what the pain points are. For example, if a lot of force is exerted on a particular component of the machine, it is likely to get damaged before the other parts if it is not well maintained. So, one should particularly focus on maintaining this part well to avoid such hassles. There is no definite strategy to predict what parts of a machine can get damaged first, but logically, the parts that endure the highest pressure or are overused a lot may be the most vulnerable.
Keep the surrounding area clean
If a machine is stored in a place filled with dust and debris, its durability will diminish. So, it is not enough to clean just the industrial machine – it is equally important to keep its surrounding areas tidy and hygienic. Regularly sweeping, mopping, and dusting the factory or warehouse is a must. Also, insects can play a major role in destroying machine components, so regular pest control is also essential to avoid these issues.
Train employees to use the machines properly
A factory’s workers and staff members use its machines the most, so they require guidance and training to use these machines correctly. Factories should organize regular staff training sessions to make workers aware of how to use industrial machinery and notice any signs of damage early on. Also, regular training sessions can help them understand the safety hazards involved in using these machines and go about with their daily tasks carefully.
Have spare parts handy
In case of a sudden malfunction, the show must still go on, so having spare parts handy goes a long way while operating industrial machines. Cylinders, fluids, sensors, bearings, and connectors tend to be some spare components a factory should always have in store.
Maintain a schedule for maintenance
Factories need to be consistent in maintaining their machinery. So, having a systematic record of maintenance, cleaning, and calibration checks of industrial machines can help ensure that factories do not miss out on regular cleaning and maintenance. It helps to maintain a spreadsheet with maintenance records of each machine added in. All details regarding the type of maintenance and the next due date should be mentioned in this sheet.